Capabilities
Diameter
200mm
Length
600mm
Hard Turning
Hard turning is a machining process that allows for the turning of hardened steel with high hardness levels of up to 68 HRc. It serves as an alternative to grinding and offers several advantages : time savings, use of standard cutting tools, the possibility of both turning and grinding on the same machine, and the ability to work on geometrically complex pieces.
For hard turning, special cutting tools made of cubic boron nitride, tungsten carbide, or ceramics are employed. These materials are extremely hard and wear-resistant, making them suitable for processing hard metals.
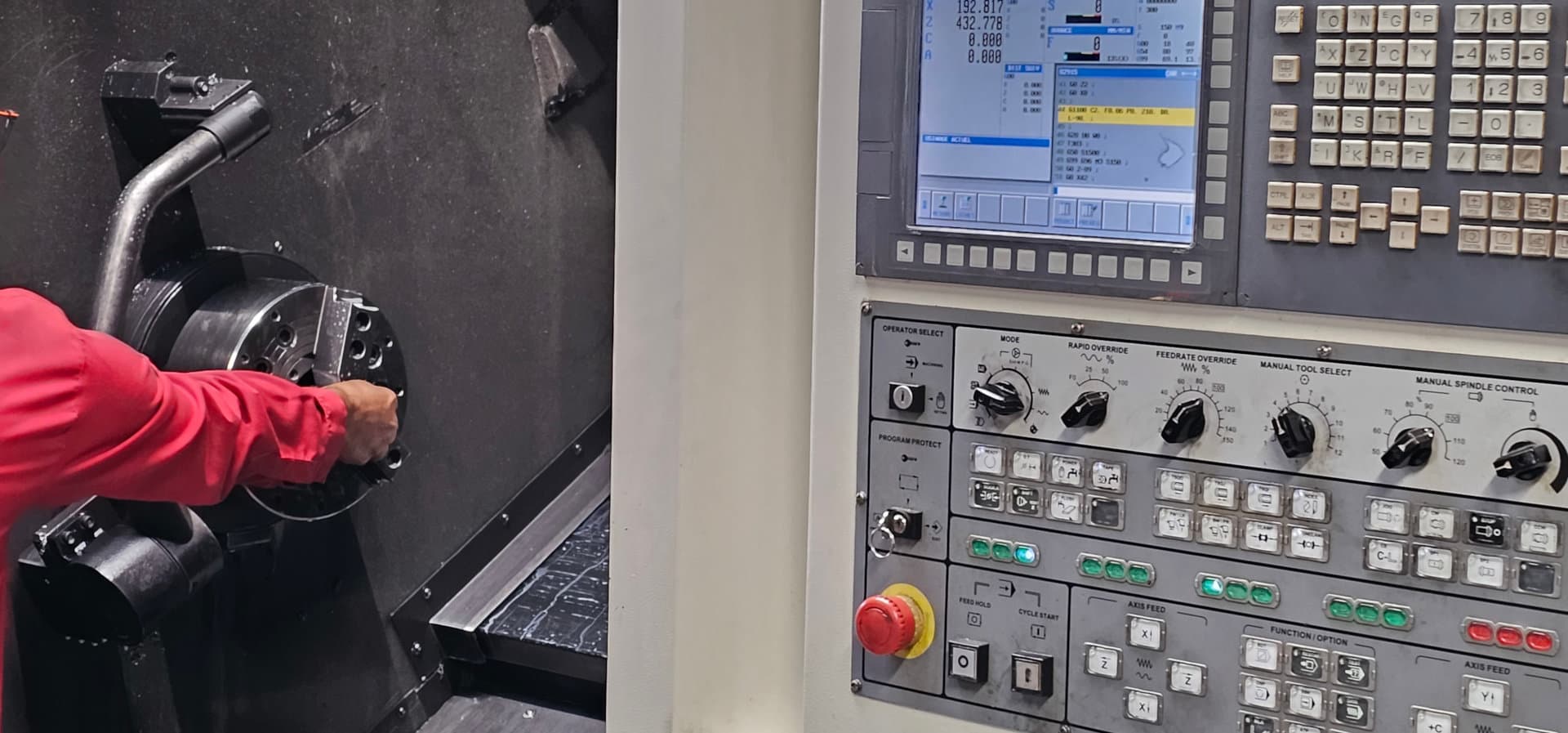
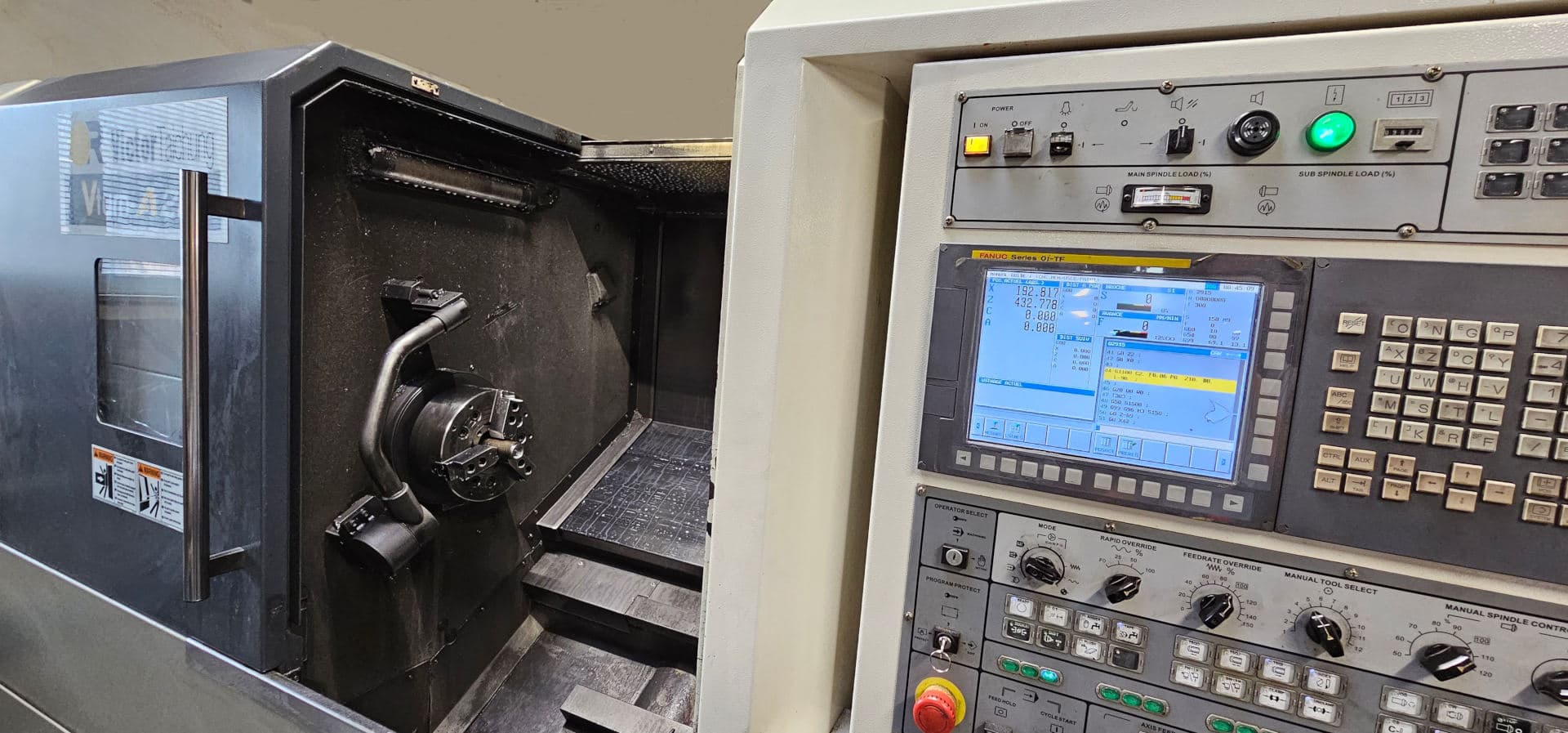
Precision Turning
Precision turning enables the precise production of cylindrical or oblong pieces (0.01 mm precision). During the turning process, the piece is secured by a chuck on the lathe, which is then set in motion. A cutting tool is then held against the rotating piece to gradually remove material and obtain the final piece. Material removal can occur both from the cylinder's exterior and interior. Our CNC lathe park allows us to create pieces up to 600mm in length and 20mm in diameter.
For any turning needs, feel free to contact our sales team, which will address your requirements promptly.
Our creations
Machined materials
Mechanical turning allows us to work with a wide variety of materials such as:
- Ferrous Metals:
- Steel
- Stainless Steel
- Cast Iron
- Ductile Iron
- Steel Alloys
- Non-Ferrous Metals:
- Aluminum
- Copper
- Bronze
- Brass
- Titanium
- Magnesium
The choice of material depends on the application and the required properties of the final piece. Other factors, such as heat and corrosion resistances, conductivity, and density, also influence material selection. Thus, we adjust our machine settings based on the need and the processed material.
Benefits of mechanical turning
The main advantage of mechanical turning lies in its ability to create round profiles. Due to its operating principle, turning ensures perfect roundness, which is more challenging to achieve in milling, for example. Mechanical turning also provides high precision, good surface finish, material versatility, high efficiency, and cost reduction compared to other machining methods.
Custom Production
Since customization is our specialty, our skilled team manufactures your pieces according to your needs and specifications. The custom piece production process proceeds as follows:
- Our sales team receives your project along with your plan via email.
- Our technical team assesses feasibility, provides advice, and prepares the cost estimate based on your needs.
- We send you the offer and remain available to answer any questions or address changes to the project.
- Once the offer is approved, we internally create all the machine programs for producing your pieces.
- We then precisely machine the pieces, paying attention to every detail.
- Your pieces are packaged on custom pallets and delivered to you.
This proven process ensures adherence to deadlines, high-quality results, and high customer satisfaction. Additionally, we remain attentive throughout the project and its post-project phase.
Applications of Turning
Mechanical turning finds its place in a wide range of industrial applications. It is extensively used to create high-precision components, including punches, dies, shafts, gears, bushings, fittings, valve parts, nuts, bolts, and many more. It also plays a crucial role in the production of tools, parts for the oil and gas industry, aerospace, automotive, medical field, as well as in the manufacturing of electrical and electronic components.